A 3-day tech show was held at the experience center of the Yanfeng Beijing Plant, showcasing nearly 30 innovations in interior and exterior, seating, electronics and safety. Different from the past, this show brought a number of low-carbon products that expemplify our sustainability philosophy in product design and development.
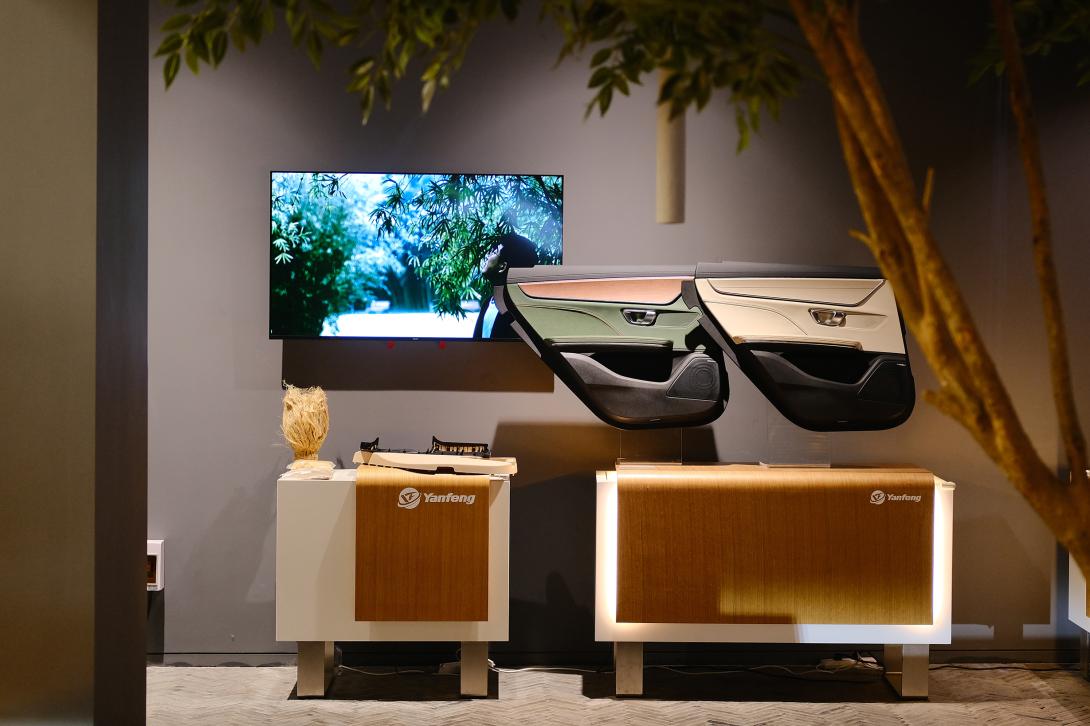
The BASSI® Bamboo Element Door Panel
The design of BASSI® Bamboo Element Door Panel came from the soothing experience with nature, oriental Zen and caring for the earth. It is the first time that we boldly implanted bamboo elements into automotive interior design as much as we can. The door panel uses bamboo veneer for the insert panel and a variety of bamboo fiber composite materials in the upper door panel, armrest, map pocket, and door panel frame, which enhances the quality of the cabin while conveying the concept of sustainability and highlighting the aesthetics of the neo-Chinese style.
Bamboo veneer is used in place of traditional wood veneer or technological veneer for the insert panels, effectively reducing carbon emissions by 30%. The unique fiber texture of bamboo veneer, compared to wood veneer and technological wood texture, combines minimalism with a unique Chinese flavor. Bamboo is hard and resilient, with a short growth cycle. It is abundant in the southern region of China and can grow more than 30 meters in three months, which is ecologically friendly compared to trees with a slow growth cycle, and can be applied to a large area of the surface of various products for cabin interiors. With a deep understanding of the features of the material, combined with modern technology, by thinning the bamboo veneer, repeatedly removing the color, after several times of sanding and splicing, not only to retain the unique bones of the bamboo temperament but also for the bamboo, a traditional Chinese material to give more possibilities for modern design.
In addition, a variety of bamboo fiber composite materials are also used in the upper door panels, armrests, map pockets and door panel frame. By adding bamboo fiber to different materials in different ratios such as 5%-50% and mixing them, it can reduce weight by up to 17% and carbon emissions by 30%. It enhances the texture of the product while naturally achieving anti-bacteria and reducing VOCs.
The Reco™ Low Carbon Seat
The Reco™ Low Carbon Seat is another important milestone in Yanfeng's sustainability strategy. Utilizing innovative and recycled materials, from foam to the steel frame, the Reco Seat’s reduces product carbon emissions by up to 40% compared to conventional seating.
A focus area of Yanfeng's sustainability strategy is the use of innovative, sustainable materials. The Reco Seat features several materials, including Polyethylene Terephthalate (PET), Polyurethan (PU) trim, recycled foam, thermoplastic foam, a green steel frame, a PET lightweight back panel, and hybrid cushion.
The PET PU trim is made from 100% recycled soft drink bottles, reducing product carbon emissions by more than 20%, and is translucent and soft to the touch. The foam used in the Reco Seat is combined with recycled and thermoplastic foam to provide improved resilience and support. Furthermore, the use of industrial wastewater steam in the foam production and molding process significantly reduces energy consumption and carbon footprint.
The seat pan is made from high-strength recycled plastic instead of a traditional metal seat pan, while the recycled steel frame, using 100% scrap steel as the raw material, together with green electricity for the production, reduces the product carbon footprint by over 60%. The seat back panel uses recycled PET to achieve a lightweight and dynamic styling. In addition, the hybrid cushion uses high strength-recycled composites instead of metal which reduces the carbon emission by 20% and allows for a wider choice of surface treatment techniques.
The ClickRim Modular Steering Wheel
The ClickRim steering wheel creatively utilizes a modular concept by designing the steering wheel with segmented housings, which allows for segmented replacement of the housings made of different materials. Whether it's fabric, leather, synthetic leather, or any other wrapped or injection-molded material, these surface materials of the steering wheel can be individually replaced by segments. The pre-installed hands-off detection and heating module and the automated wrapping process provide efficiency to the production.
All components of the ClickRim steering wheel are also made of recyclable materials. Thanks to the modular design, components can be easily disassembled and returned to the material cycle. The metal armature, the spacer fabrics as well as the surface material can all be recycled. The reduction of conventional foam in the wrapping process enables us to reduce CO2 emissions by 1 kg per steering wheel.
While traditional steering wheel wraps utilize a complex handcrafted process that takes an average of about 60 minutes to produce a single steering wheel, ClickRim's innovative design saves about two-thirds of the production time per steering wheel, dramatically improving the efficiency of steering wheel assembly and in turn reducing the carbon footprint of the manufacturing process.
ecoSkin® Innovative Interior Surface Technology
Yanfeng has been actively exploring the development and application of sustainable surface materials in recent years. ecoSkin, as a representative, has unique environmental benefits that can effectively reduce the VOC in the car and create a green and eco-friendly cabin experience.
Made from a recyclable thermoplastic elastomer (TPE), ecoSkin can be applied to most of the visible surfaces of interiors in the cabin. With a lifelike texture in the surface, it has a delicate feel and is easy to clean due to its high stain-resistance. Compared with traditional wraps, the innovative material has more freedom of molding as there is no restriction on the R-angle. Not only does it offer customizable color combinations, but it also allows for light transmission as needed, while the integrated multi-texture process greatly shortens the manufacturing process and reduces the carbon footprint in manufacturing. As the production is solvent-free, VOC emissions can be greatly reduced, making it an extremely environmentally friendly product.
The latest wireless charging module uses ecoSkin surface technology as a whole, demonstratingn how the same material can be applied in different ways on a single product, such as the combination of different color schemes and light-transmitting, etc.
Through a one-piece injection molding process, the overall weight reduction is as high as 37.5%, which is another innovative achievement of ecoSkin to realize both high quality and low-carbon footprint.
In addition to the above products, the technical event also showcased a series of industry-leading products, including the CYMATICX Sound Flow Cabin that brings immersive audio experience, the Hover™ SPA Seat that is the industry's first zero gravity seat to use a four-way electric independent adjustment of the upper backrest, the WAVE Electric Air Vent Module that realizes a variety of innovative wind modes, such as "natural wind," "ultra-large sweeping wind," and "feather wind," as well as an Ultra-low Latency E-Mirror. The event attracted a great number of customers and media, established a great opportunity for in-depth exchanges and received very positive feedback.
About Yanfeng:
Yanfeng is a leading global automotive supplier, focusing on interior, exterior, seating, cockpit electronics, and passive safety, and is exploring new business actively. Yanfeng has more than 240 locations and approximately 57,000 employees worldwide. The technical team of 4,100 experts is in 14 R&D centers and other regional offices, with complete capabilities including engineering and software development, styling, and test validation. Focusing on Smart Cabin and lightweight technology, Yanfeng supports automakers to explore future mobility and provide leading cabin solutions.
Press Images
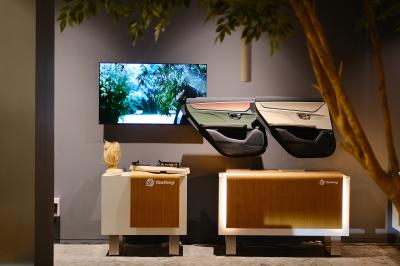