Yanfeng Automotive Interiors, the world’s largest supplier of automotive interiors, is presenting a new direct back-foaming process for genuine or synthetic leather instrument panels at the 2015 International Motor Show (IAA) in Frankfurt. The optimized, streamlined production process from Yanfeng Automotive Interiors ensures the high-quality leather wrapping of instrument panels. This means that in the future, leather-wrapped and conventionally covered instrument panel surfaces can be handled on just one production line using the same tool. This production process can also be applied to door panels.
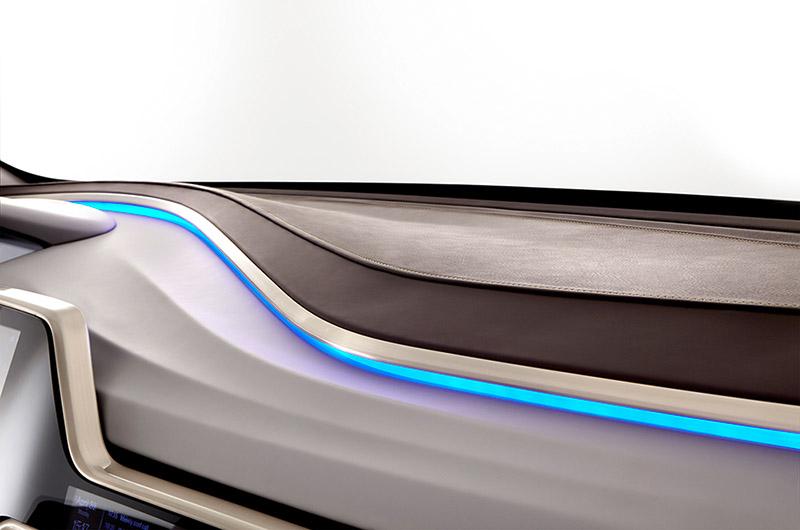
Leather-wrapped instrument panels can now be manufactured on one production line, where other surface materials such as conventional skins also can be back-foamed. By introducing this new production process for making leather-wrapped instrument panels – whether genuine or synthetic – Yanfeng Automotive Interiors can reduce the amount of tools used in the future by 50 percent. The company is therefore not only reducing tooling and process costs, but also facilitating and increasing the potential for customization in cockpit production.
Genuine leather, synthetic leather, thermoplastic polyolefins and slush skins have become standard surface materials in cockpit production. The different surface concepts have led to multiple-stage production processes. Each variety requires a specific tool, which results in high processing costs. This is where Yanfeng Automotive Interiors’ new production process for direct back-foaming of leather comes in as a standardized solution for producing conventional and leather-wrapped instrument panels. Both versions are identical in shape and exhibit the same component thickness in both basic synthetic and premium leather versions, making this possible. Regardless of whether synthetic or genuine leather is used to finish the instrument panel, the production process is the same.
Direct back-foaming of leather – an automotive industry first
The process of direct back-foaming involves back-foaming the sewn covering directly with polyurethane (PUR) foam. To prevent the PUR foam from passing through the small sewing holes, the sewn covering is coated with a thin film on the back. This procedure enables the sewn covering and the film to be inserted into the foam tool and back-foamed in one step.
“We managed to optimize the combination of leather covering, pre-formed film and foam to achieve an all-round, premium-quality surface. We were also able to improve the quality of the leather covering and precision of the visible stitching to an unprecedented level,” said Dr. Oliver M. Becker, executive director, process innovation, Advanced Product Development & Sales, Yanfeng Automotive Interiors. “The spotlight is on the flawless appearance and feel of the leather covering, which shows no signs of seam line disturbance or of the “orange peel effect” in the leather grain, which is a common flaw today.”
This patent-pending production process is now ready for series production.
Three-dimensional reliefs thanks to leather molding
In addition to the back-foaming process for leather, Yanfeng Automotive Interiors is also developing a new leather component production process. This process involves inserting precut, uncoated leather into a back-molding tool and injection mold behind it with thermoplastic. The high internal mold pressure enables the leather to be shaped three-dimensionally and embossed with a pattern. This creates highly defined surface structures and patterns. Once back-molded, the component is lacquered. The result is a hard leather covered surface with extraordinary reliefs.
“From a technical perspective, creativity has no bounds when it comes to combining colors and materials,” said Becker. “However, this creates price-driven obstacles in cockpit production. The main issue for suppliers is how much variety can be produced economically, which is a challenge we aim to resolve through continuous process innovation.”
About Yanfeng:
Yanfeng is a leading global automotive supplier, focusing on interior, exterior, seating, cockpit electronics, and passive safety, and is exploring new business actively. Yanfeng has more than 240 locations and approximately 57,000 employees worldwide. The technical team of 4,100 experts is in 14 R&D centers and other regional offices, with complete capabilities including engineering and software development, styling, and test validation. Focusing on Smart Cabin and lightweight technology, Yanfeng supports automakers to explore future mobility and provide leading cabin solutions.
Europe, South Africa and North America
Media Contact
Press Images
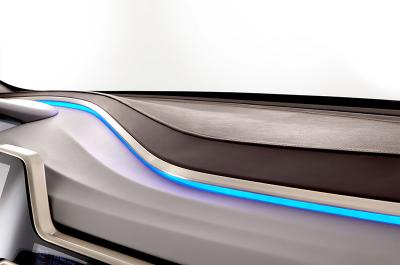