Tour around our Neustadt plant
What does Yanfeng Automotive Interiors (YFAI) manufacture in its Neustadt plant? Approximately 100 visitors were able to get a firsthand look. The plant exclusively opened its doors to the participants of a large, two-day conference on automotive interiors that took place in nearby Regensburg.
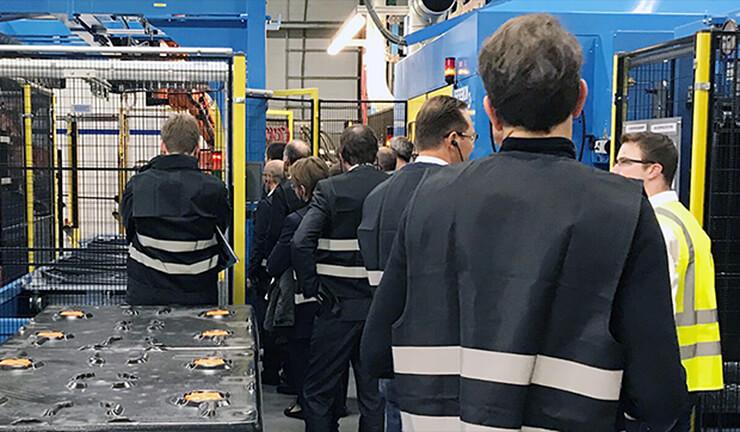
Yanfeng Automotive Interiors globally produces door panels for all automotive brands and all vehicle segments, from the small car segment via the mid-range to the upper and premium class. The Neustadt plant has about 800 employees and manufactures door panels, armrests and instrument panels. During their tour at the Neustadt plant, visitors saw production of door panels for the BMW 3 and 5 series. Conference participants learned about the structure of door panels and gained an overview of the various process technologies that play a role in the production. The plant has more than 200 independent process devices and 75 robot systems. These include the system for a new compression molding process (ChyM), which is used to manufacture weight-saving door panels for the BMW 5 Series. In addition to the door panels for the limousines and Touring estate versions of the BMW 3 and 5 series, the location also produces instrument panels for the Mercedes-Benz B-Class. The plant site is a total of 54,000 square meters, half of which is production and warehouse space.
Tailor-made customer solutions rely on sustainable raw materials
The plant tour started with an overview of the production line for the BMW 3 Series door panels. The non-visible elements of the door panels for the limousine and Touring versions are mainly manufactured from wood fibers. The visitors were able to see how natural fiber mats are pressed and the natural fiber substrate is back molded with plastic. This innovative production process makes the door trim much lighter. The material and leather covers on the elegant trim are attached using another innovative process - groove lamination. The edges of the covers are pressed into grooves, making an additional component unnecessary. This saves additional weight.
“As a supplier to the global automotive industry, we rely on sustainable and environmentally friendly raw materials,” said Wolfram Brüning, plant manager of the YFAI plant in Neustadt. “With high-quality and light components we support our customers in making the interior sustainable, saving weight and lowering consumption.”
New compression molding process for door panels reduces weight
The next stop on the tour was to observe door panel production for the BMW 5 Series that uses a hybrid compression molding (CHyM) process. This patented technology made its European debut at the IAA four years ago. The CHyM compression molding process for manufacturing door panels combines the advantages of natural fiber components and thermoplastic injection molding. The interior components produced by this method are 40 percent lighter.
“Our innovation management aims to develop technologies that further drive sustainability and lightweight construction. Our experience with natural fibers enables us to develop products that meet the changing requirements of our customers and the industry,” explained Brüning.