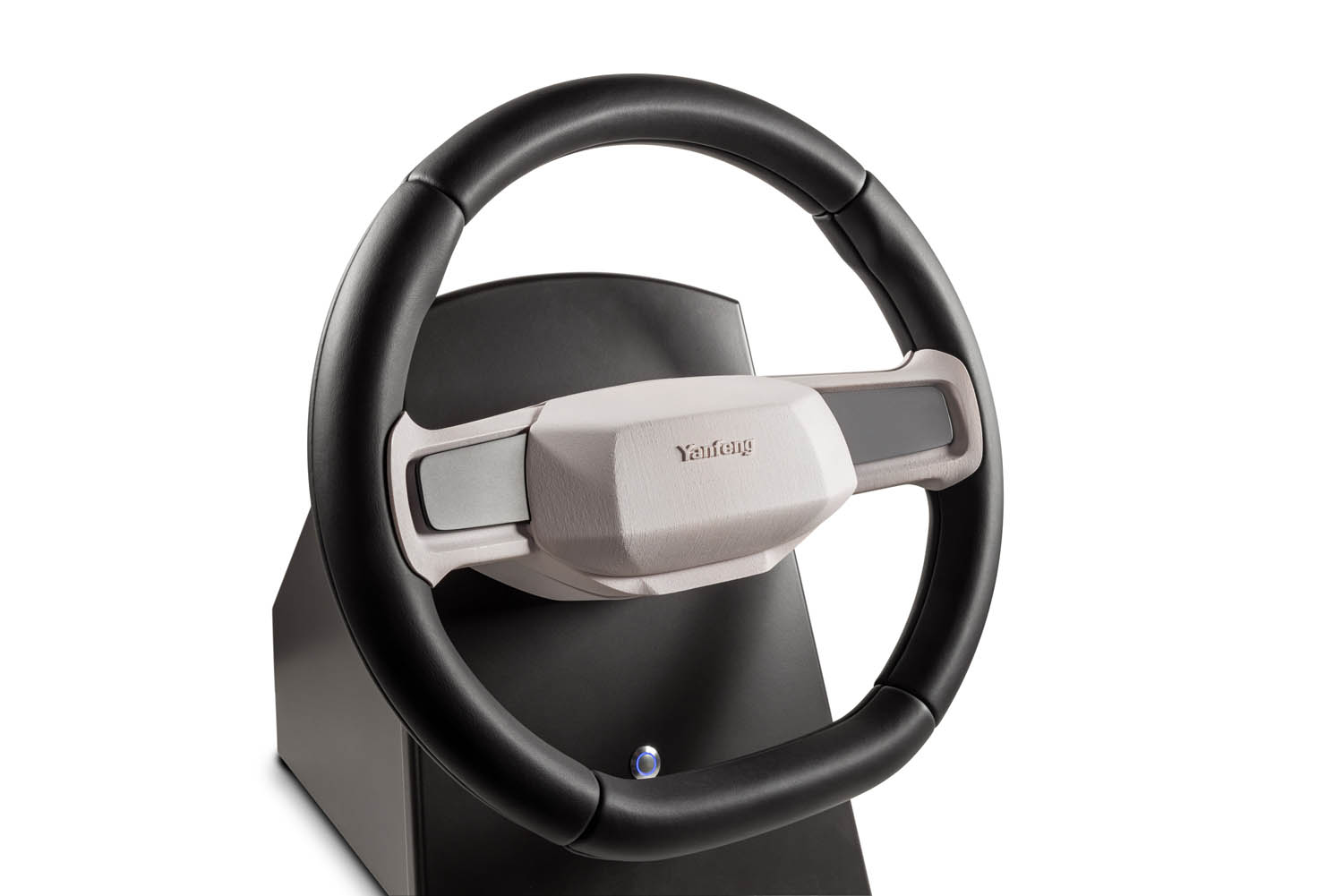
Press Kit
Yanfeng to showcase new modular steering wheel concept at CES that reduces production time and CO2 emissions
Steering wheel innovation makes world premiere at CES
LAS VEGAS – January 8, 2024
Yanfeng is setting new standards in design and production with the modular steering wheel concept ClickRim, which is making its debut at the 2024 CES. Whether fabric, leather, artificial leather, or any other wrapped or molded materials – these surface materials of the steering wheel can be individually tailored to meet specific requirements thanks to the changeable segments. This steering wheel is more than just a design feature however, as all components used are also recyclable.
The production of a steering wheel is extremely time-consuming and labor-intensive. It takes approximately 60 minutes on average to manufacture one steering wheel. The wrapping process accounts for most of this production time because traditional steering wheels are wrapped using a complex, manual process. This involves applying a foam coating to the metal skeleton of the steering wheel, followed by bonding a heating mat and finally the wrapping of the surface material. Each and every step, no matter how small, requires precise manual processing.
From manual production to a fully automated process
The ClickRim modular steering wheel concept involves the development of individual segments or half shells that are clipped onto the steering wheel rim and connected to each other. Anything is possible – whether there are two, three or four shells, alternating between wood and leather, fabric or natural fibers. The highlight: all the lighting and hands-off detection functions, as well as the heating mat, are pre-assembled and integrated directly into the shells.
Yanfeng has made this possible through a new manufacturing process that combines two production steps. The company has developed a process in which the shells are wrapped fully automatically with spacer fabrics and leather. The injection-molded part is already wrapped with the spacer fabric and fitted with the heating mat. The automaker's logo or the vehicle model branding can also be integrated directly into the shell during the wrapping process. The decorative or connecting seams on the steering wheel cover are no longer required – but could be added if required.
The overall complexity of the steering wheel product scope is also significantly reduced.
“Our new automated wrapping process allows us to save around two-thirds of the conventional production time for each steering wheel while maintaining efficient costs,” said Patrick Nebout, Chief Technology Officer at Yanfeng Technology.
The company's innovation team worked cross-functionally across Germany, North America and China on the development of the concept for this new, modular steering wheel.
“Through the cross-business unit collaboration between our interior, electronics and passive safety product departments, we are able to rethink and reorganize processes,” added Nebout.
ClickRim is part of Yanfeng's Circular Steering Wheel
Recycling and maintenance of steering wheels has previously been somewhat complex. Thanks to the modular design of the new steering wheel, the individual components can be disassembled easily and returned to the material cycle. The metal armature, the spacer fabrics as well as the surface materials used can all be recycled.
“With each new development, we are faced with the challenge of taking a holistic view of a product's life cycle – from the product design to the manufacture and use of the product at the end of its life, right through to the return of individual materials into the cycle,” Nebout said.
The use of spacer fabrics instead of conventional foam in the wrapping process for steering wheels will enable Yanfeng to reduce CO2 emissions by 1.0 kg per steering wheel.
The new steering wheel has passed all standard prototype tests, including head impact and body block tests. ClickRim is aimed at the premium and mid-range segment. This close-to-series concept development is ready to be used in the next generation of vehicles in model year 2025.